High precision metal folding methods
Client: RoboFold
Consultant: Dr Daniel Balint, Department of Mechanical Engineering
Expertise: Finite element modelling
Our consultants shared their expertise in finite element modelling to help RoboFold take their RoboFold system into mass production.
The Context
RoboFold is a unique, low carbon manufacturing system that uses robots to create curved metal forms. All the information needed to create a shape is held in the cutting and movement of the robots, which are programmed to manipulate sheet metal by folding it along pre-scored curved lines.
Taking inspiration from other digital fabrication technologies, such as 3D printing, the entire RoboFold process is simulated in computer aided design (CAD) software. RoboFold has generated interest across the architecture and interior design sectors since its launch in 2008, and is now providing training in its system for the production of architectural cladding, art installations and bespoke furniture.
The Challenge
To move into mass production, the RoboFold system needed to perform with greater precision. Although each metal sheet is manipulated directly by the robots, other factors can distort its deformation, such as the elastic recovery of the material, the gripping position of the robots and the scoring technique. These factors needed to be accurately accounted for in mathematical models that determine the folding paths taken by the robots.
The Solution
Gregory Epps, Managing Director of RoboFold and an alumnus of Imperial College, sought out Dr Daniel Balint, a material deformation expert with experience in finite element modelling.
I applied for support through Knowledge Connect, which provides funding for London-based SMEs to harness the research expertise of a university to help develop a product. From my days as an Imperial student, I knew that Dr. Daniel Balint was the only one with the expertise and experience we needed.
Gregory Epps
Managing Director, RoboFold
Dr Balint is Co-Director of Imperial’s metal forming and materials modelling research group, part of the Mechanical Engineering Department, which looks to form an understanding of the fundamental aspects of material deformation and apply it to industry problems:
I was interested in RoboFold’s idea of folding metal sheet like paper in order to produce complex shapes, and could immediately see how finite element simulations would benefit their process. It is a pleasure to work with entrepreneurs like Gregory Epps, and carry out consulting that contributes to the evolution of small businesses.
In order to optimise the RoboFold forming process, I established a set of finite element models to predict the bending and springback of a scored metal sheet under the action of robot folding. These models were used to optimise the score depth and shape, the number of vacuum grips and their locations and spacing, with respect to the accuracy of the final part, its structural integrity and the residual stresses at the score line and grip locations. The finite element models were delivered to RoboFold in order to establish a simulation capability at the company that will be used for further studies of robot sheet metal folding.
Dr Balint
Co-Director, Department of Mechanical Engineering, Imperial College London
The Impact
Gregory is now able to integrate these models into his CAD software, to improve the precision of the RoboFold manufacturing system.
The flexible and short-term nature of consultancy meant that RoboFold could access the specialist expertise it needed on realistic, affordable terms. Gregory is confident that with further research, through consultancy, there is potential for RoboFold to expand.
The more we are able to refine our models, the closer we get to being able to mass produce product designs. This will also enable us to move into new markets, including the automotive and aerospace sectors, where high precision is essential.
Gregory Epps
Managing Director, RoboFold
Share post:
Related case studies
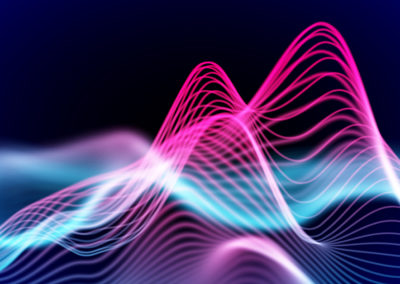
DISPERSE: Making sense of sound waves
Disperse is an interactive software package for studying guided sound waves in a wide range of structures and components. Its principal applications are the exploitation of guided waves for non destructive evaluation across all industries including aerospace, power generation, and oil and gas. read more
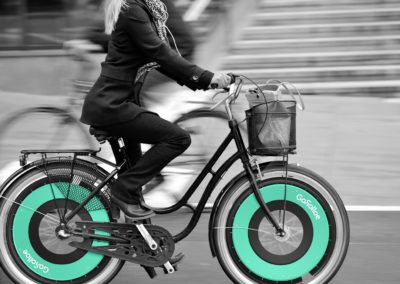
GoRolloe Life Cycle Assessment
Our consultants provided life cycle analysis for GoRolloe, a start-up developing a device for bicycle wheels that filters out air pollution as its riden, helping the company identify potential environmental hotspots, and improvements. read more
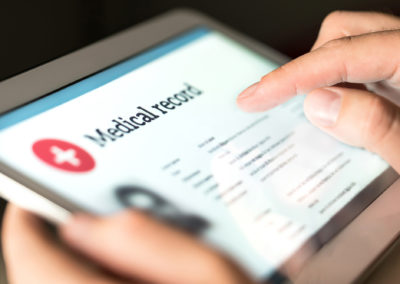
Global adoption and regulation of electronic medical records
Our consultants shared their expertise in clinical medicine to help IMS Health to assess the adoption, governance and regulatory landscape of electronic medical records (EMR) at different levels of healthcare systems around the world. read more